Bagh Printing: The Block Printing Legacy of Madhya Pradesh
- Akanksha Shukla
- Dec 1, 2024
- 5 min read
Updated: Dec 2, 2024
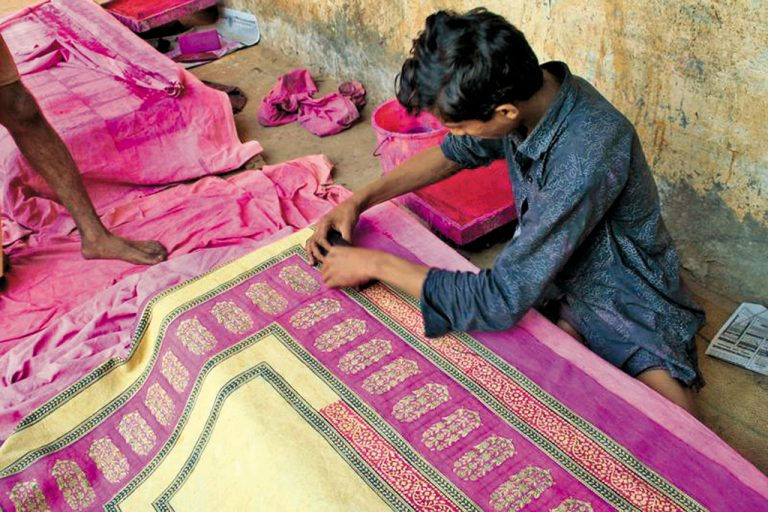
Bagh Printing is a traditional hand block printing technique celebrated for its geometric and floral compositions. Using natural colors, particularly striking shades of red and black on a white background, this craft is rooted in the quaint village of Bagh, situated along the Baghini River in Madhya Pradesh’s Dhar district. Its name derives directly from this serene setting, which has played an integral role in shaping this exquisite art form.
TABLE OF CONTENTS:
The History of Bagh Printing:
The craft’s history is deeply intertwined with the journey of the Muslim Khatri community, who migrated from Larkana in Sindh (now Pakistan) to Marwad in Rajasthan, and later to Manawar before settling in Bagh in 1962. These artisans brought with them the Ajrak printing traditions of Sindh but adapted them to local materials, tastes, and resources, creating a unique art form now known as Bagh Printing.
The printing process is as meticulous as it is artistic. Fabrics, typically cotton or silk, undergo an intricate treatment involving a blend of corroded iron fillings, alum, and alizarin to prepare them for block printing. The Baghini River’s mineral-rich waters play a vital role in this process, enhancing the luster of the fabric while locking in its natural colors. The entire process, encompassing pre-printing, printing, and post-printing stages, results in vibrant, visually stunning textiles that are sought after worldwide.

The Influence of Bagh on Its Craft
The region’s geography and history have significantly shaped the craft. The Bagh Caves, ancient Buddhist rock-cut structures, have inspired many of the intricate designs seen in the textiles, with patterns echoing frescoes and motifs from these historic sites. The Baghini River, central to the craft’s water-intensive processes, has a distinct chemical composition that contributes to the vibrant, long-lasting hues characteristic of Bagh prints.
The Labor intensive and elaborate Process of Creating Bagh Prints
Bagh printing, a meticulous craft rooted in tradition, involves several intricate steps. The process not only demonstrates the skill of artisans but also their deep connection to nature and heritage. Here's a detailed overview of the process of creating Bagh Printing:
Raw Materials
Bagh printing uses a variety of fabrics, including fine cotton (mulmul), Maheshwari cotton, Kosa silk, chiffon, crepe, georgette, and mulberry silk. These materials are selected based on specific orders, catering to diverse needs, from saris and dupattas to yardage for bed covers. Wooden printing blocks, sourced from renowned centers like Pethapur in Gujarat, Gandhinagar, and Jaipur, are engraved with intricate patterns that reflect traditional motifs.
Natural ingredients such as Cenchura (raw salt), castor oil, goat dung, alum, iron sulfate, pomegranate rinds, tamarind seed powder, and leaves of plants like indigo and Dhavdi are crucial for dye preparation. The dyes—predominantly black and red—are derived from a mix of natural elements, with alizarin ensuring vibrant red tones.
Pre-Printing Process
Before printing, fabrics undergo rigorous cleaning to remove starch and impurities. This involves soaking them in the river, beating them against stones, and sun-drying. This step is critical to prepare the fabric for uniform dye absorption.
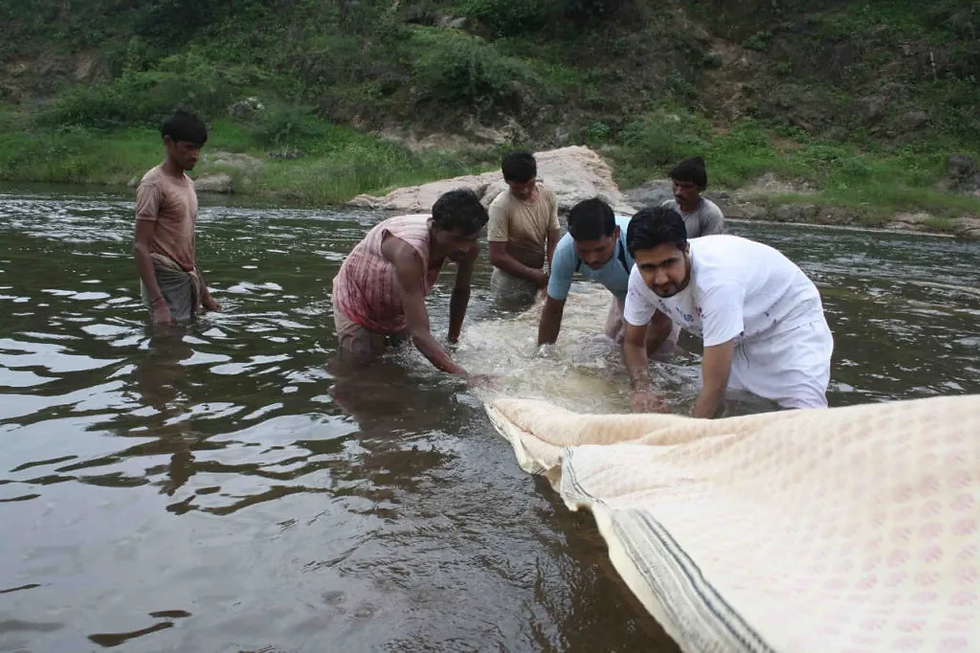
The Bhatti Process
Once cleaned, the fabric is treated in a boiling mixture of alizarin, Dhavdi flower roots, and water for about four hours. This immersion ensures that the cloth acquires a base dye and becomes soft and pliable for printing. Following this, the fabric is soaked overnight in a blend of goat dung, castor oil, raw salt, and water. This unique mixture helps enhance the cloth's ability to absorb natural dyes effectively.
After soaking, the fabric is dried on inclined surfaces to allow uniform exposure. It is then rinsed thoroughly in flowing river water to achieve a clean surface, ready for printing.


Printing Process
The heart of Bagh printing lies in its hand block printing technique. Using a wooden tray (locally known as paliya), artisans prepare black and red dye pastes. The fabric is stretched over a padded surface, and the wooden blocks—coated with dye—are pressed onto the cloth with precision. Each block represents a specific design, and artisans repeat patterns meticulously across the fabric.
After printing, the cloth is dried for several days to let the colors set. The final steps involve rinsing the fabric in the flowing waters of the Bagh River and immersing it in a solution of Dhawadi flowers and alizarin. This imparts a sheen and ensures that the colors become vibrant and long-lasting.

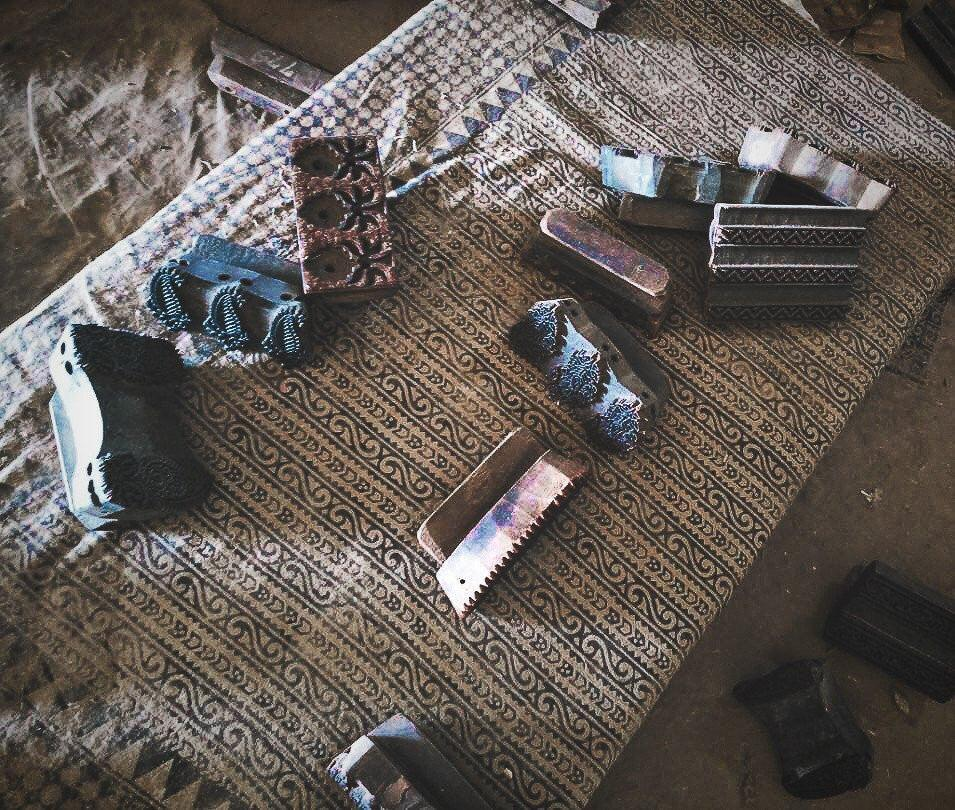
Finishing Touches
Silk fabrics require double the time and care compared to cotton, reflecting the labor-intensive nature of the craft. Once completed, the Bagh print textiles radiate with intricate patterns and vibrant natural hues, embodying the artistry of the region.
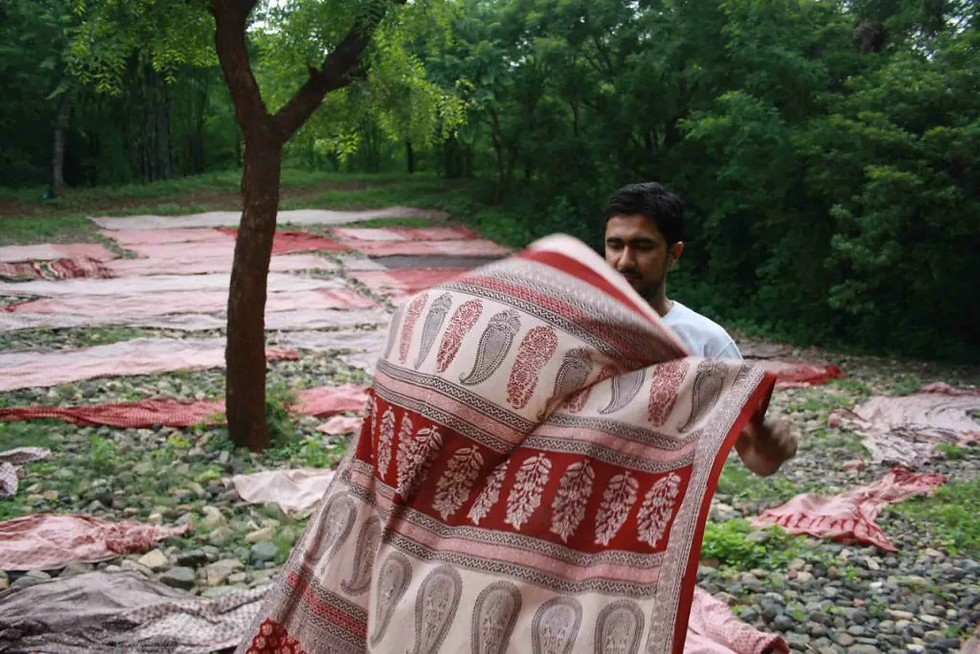
Application and Innovation
Initially, Bagh printing catered to local tribal communities like the Bhil and Bhilala, creating distinct garments based on cultural identity. Over time, artisans like Mohammed Yusuf Khatri and his family adapted designs to appeal to urban and international markets. This innovation led to block printing on diverse materials, including bamboo mats, leather, and jute, showcasing the craft's versatility. Bagh printing on bamboo mats, for instance, became a global novelty.
The careful balance of tradition and innovation has allowed Bagh printing to retain its essence while meeting modern aesthetic preferences, making it a treasured craft both locally and globally.
A Geographical Indication of Pride
In recognition of its uniqueness and cultural significance, Bagh Printing has been awarded the Geographical Indication (GI) tag in 2016, safeguarding its heritage and ensuring authenticity. This status not only celebrates the craft but also supports the livelihoods of its artisans by differentiating it in global markets.
Exploring Bagh Printing Through Craftique Hub
One of the best ways to support Bagh Printing is by experiencing its magic firsthand through our carefully curated craft tours. At Craftique Hub, we offer the "Heritage Textile Trail of Madhya Pradesh", which includes immersive visits to the hubs of Maheshwari, Bagh, and Batik printing. These journeys allow participants to witness the art form in its birthplace, interact with artisans, and purchase authentic creations directly from them.
To learn more about our tours or inquire about customized experiences, visit the Craft Tour section on our website or write to us for details. By joining these tours, you not only celebrate India’s cultural richness but also contribute to the preservation of its traditional arts and the livelihoods of its artisans.
Conclusion
Bagh printing is not merely a craft; it is a confluence of heritage, nature, and artistry that has stood the test of time. From the meticulous process of preparing fabrics and dyes to the final step of creating intricate patterns, it reflects the dedication of artisans who have carried forward this legacy for generations. The rich interplay of natural materials, the unique qualities of the Bagh River, and the cultural influence of ancient traditions have all contributed to making this craft an iconic representation of Madhya Pradesh’s textile heritage.
Today, as Bagh printing continues to evolve with contemporary designs and applications, it remains a testament to the ingenuity of its craftsmen and the enduring appeal of sustainable, handmade art. By supporting initiatives like craft tours, purchasing directly from artisans, and celebrating their stories, we can ensure the survival and growth of this beautiful tradition. Let us preserve this art form, which is not just a symbol of Indian heritage but a vibrant bridge connecting the past with the present and future.
Let’s journey together to keep this timeless art alive!
Comments